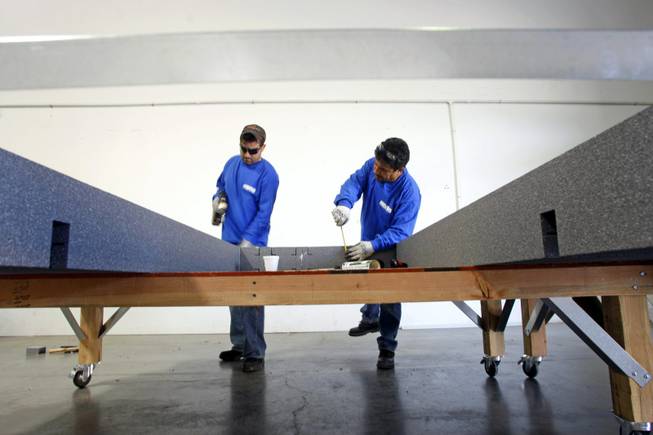
Todd Johnson, left, and Bill Montano, employees of Kama Energy Efficient Building Systems, assemble a prefabricated building section at the company on Oct. 6.
Friday, Nov. 6, 2009 | 3 a.m.
Sun Coverage
Beyond the Sun
The recession isn’t slowing down Ken Miller, an energy-conscious entrepreneur who has developed prefabricated walls he says cut down energy use by 30 percent.
“We’re just inundated,” he said of the demand for his product.
Miller, who owns Kama Energy Efficient Building Systems with his wife, Alaina, created K-tect about three years ago after becoming increasingly dissatisfied with wood’s heat retention.
Wood represents about 25 percent of a house’s frame, with cotton-like insulation filling the rest of the space.
“There’s got to be a better way,” he said.
Miller is forgoing wood stud framing altogether in lieu of steel and the fluffy, itchy insulation for a lightweight, compressed Styropor insulation in mild climates, or Neopor, a product made of cellular lightweight concrete in warm climates like Las Vegas.
Builders bring Miller their plans, and his workers build the walls — doors and window cutouts included — to the architect’s specifications. All a worker at the home site has to do is stand the wall up and mount it to the floor and adjacent walls.
“We’re not reinventing anything,” he said. “I just put it together differently.”
Miller has been in the construction business for 40 years, starting out as a jack-of-all-trades, but quickly becoming a carpenter.
He worked on Bellagio’s Spa Tower for a year, deciding afterward to return to building houses for its more personal and faster pace.
But after working with steel and the higher quality building materials used in commercial buildings, Miller was no longer satisfied with sandwiching insulation between heat-retaining wood studs.
He decided to use steel for the studs, and although he concedes that steel retains more heat than wood, he said the insulation he uses — Styropor and Neopor — doesn’t invite mice, roaches or mold.
The building slowdown has actually benefitted Miller’s company because, he explains, builders are no longer scrambling to put up houses as fast as they can. This recession is giving them a chance to reassess how they build homes — and Miller thinks they’ll want to build smarter.
“There was no impetus to change,” he said. “But now, it’s broken.”
Kama’s year-over-year growth is 300 percent, and he’s having to hire more workers to keep up with demand. By the end of the year, he expects to more than double the number of workers from five to 12.
For the past three years, Miller has been working with SCORE, a volunteer organization of retired executives that counsels small businesses and entrepreneurs.
“We’re just very proud of them,” SCORE counselor Ross Lagattua said. “It’s unbelievable.”
Architects for Charity of Texas founder Mario Morales said he decided to use Miller’s pre-fab walls for low-income homes he’s building to help the people moving into his homes afford their energy bills.
“It’s an opportunity for a smarter home,” he said.
Morales had brought his construction manager, Jerry Cabazos, to Las Vegas with him to get a feel for how the walls are installed.
“They’re put together like a puzzle,” he said.
And because the pre-fab walls are lightweight, it will also make it easier for volunteers and the people buying the houses to install them.
Miller may be on to something here. As architects are challenged to reduce the amount of greenhouse gases their buildings produce, Miller’s wall could help tip the scale in their favor.
The U.S. Green Building Council says that buildings represent 38.9 percent of the United States’ main energy use and accounts for 38 percent of all carbon dioxide emissions.
The walls, with their insulation made of recycled materials, can cut heating and air conditioning use by a third, he said.
Join the Discussion:
Check this out for a full explanation of our conversion to the LiveFyre commenting system and instructions on how to sign up for an account.
Full comments policy